What is a torque meter?
A torque meter is an instrument
which measures the torque applied to a shaft by a prime
mover. Consequently
it provides also the measurement of the actual delivered power by
the prime mover itself. Usually the instrument determines also the
speed and the direction of rotation of the shaft.
Moreover, if the torque
meter is interfaced to a flow meter which calculates the fuel
consumption of the prime mover, the system can determine
instantaneously the specific fuel consumption of the prime mover,
thus giving useful indications for a more economical
management of the mechanical system (e.g. optimal
performance profiles can be determined). In this way it is possible
to verify (even with automatic alarms generation) if the prime mover
is using more fuel with respect to the
figure specified
in its data sheet and so requires periodical maintenance, overhauling, etc… Following these indications
maintenance can be planned more accurately and fuel consumption can
be optimized.
-
LTM2214 laser torque metering system
description
The LTM2214 laser torque metering system consists of
two slitted discs fixed firmly to the rotating shaft. Through the
slits of both discs passes a laser beam which then hits the
optical receiver at the opposite side.
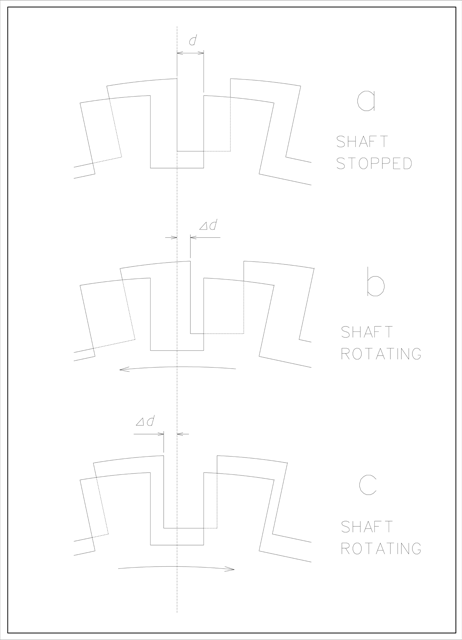
-
The duration of the
intervals during which the laser beam hits the receiver target
varies with the torque. Starting from this measurement, an
electronic system calculates torque, shaft power and various other
useful parameters (RPM, total revolutions, etc…).
-
Compared to the
preexistent technological solutions, the LTM2214 system is more
accurate (the laser gives a higher accuracy and resolution of the
measurement because the pulse shape is perfectly squared) and more
reliable as there aren’t, as in the other systems, slip rings or
radio transmitters mounted on the shaft and thus subject to
stresses, vibrations, centrifugal forces, etc… Moreover the usage of a single laser
beam eliminates completely the necessity of toothed wheels pick ups alignment, which is necessary in the systems based
on magnetic/optical pick ups or based on indipendent, or non
aligned, laser beams (e.g. systems based on fiber optics guided
laser beams with optical transducers positioned close to each
disc).
- Moreover as the
discs are
dynamically balanced and, as there aren’t other
components mounted on the shaft, the LTM2214 system can be used
even in mechanical systems with high shaft rotational speeds.
-
The fundamental advantage of this torque meter
typology is that it does not require any shaft line interruption
and can be installed whenever necessary without any modification
to the shaft line, differently from strain gauge torque meters
which may
require shaft line interruption thus increasing dramatically
installation costs and reducing system reliability. LTM2214 is thus the ideal instrument also for
retrofit installations where the existing shaftline must not be
modified in order to keep installations costs and time
low. This torque
meter typology does not allow the measurement of static moments.
-
The system can store
the measurements on a PC readable
SD Card (FAT32 formatted). Stored data can be downloaded to a
remote PC for the postprocessing (e.g. measurements can be used as
a guideline for programmed maintenance planning, to verify the
wearing of the engine or to determine the power to install on
similar plants under development).
-
-
With serial
interfaces (RS232 and RS422) it is possible to download the
measurements in real time sending them to a remote PC or to an
automation plant.
-
-
Dedicated
outputs for alarm and warning signalling of RPM, torque, power,
fuel consumption, specific fuel consumption, total revolutions,
and energy are present (potential free contacts).
Alarms
and warnings are also transmitted via serial lines. A buzzer
for acustic alarms is also present.
-
Overview of
the other
torque metering technologies
Presently
other
typologies of torque meter are present on the market.
1) The best know one (because of its old
technology) is the strain gauge type,
in which the
strain gauges are fit on the shaft with a
special glue. The variation
of resistivity of the strain gauges is processed by the electronics (mounted on the shaft) and the measurement
obtained is sent to the control station by means of slip rings or
radio waves. The limitation of strain gauges technology stays in the
difficulty of a perfect adjustment of the strain gauges, in the low
reliability of the electronics mounted on the rotating shaft and in the
slip rings/radio waves used to transmit data.
The periodical adjustment verification and its drift with the
passing of time and with temperature variations are problems which
must be seriously taken into consideration
To overcome all these issues more recently
instruments were introduced whose installation requires the
interruption of the shaftline continuity. Despite the improvement
of the accuracy of the measurement achieved by this typology of
instruments, they have the serious drawback of shaft line
mechanical interruption, which is not acceptable in many
applications where the reliability of the mechanical system is of
the utmost importance (e.g. ship propulsion, military
applications, etc..). Retrofitting is not the first choice
due to high installation costs and the long downtime required for
the installation. As a matter of fact the interposition in the shaftline of such kind of instrument mechanically weakens the
shaft line and increases the probability of failures. Strain gauge
torque meters can measure also static moments. This
technology is not applicable to high speed shafts because of the
high centrifugal forces to which the shaft mounted electronics is subject.
-
2) Another typology is
the one using magnetic/optical pick ups. Essentially the system is
composed of two toothed metal discs mounted firmly on the shaft.
With the torsion of the shaft the phasing of the electrical pulses
generated by the two pick ups varies. The phasing of the pulses is
then processed and the measurement is obtained. With this technology the
reliability issues of strain gauges systems is resolved, but an
error due to the difficulty of setting the correct phasing of the
pick ups with respect to the toothed discs is introduced. Moreover
the width and the shape of the pick ups pulses are influenced by
many factors (distance from the toothed discs, temperature,
vibrations, etc..) which alter the measurement. The fine adjustment
of the instrument to compensate the variation of pulses shape is an
issue. If the adjustment is not carried out correctly, important
errors may arise. To avoid these problems systems based on
magnetic/optical pick ups requires that the two discs are mounted at
a considerable distance (several meters), thus rendering the system
not practical, and moreover exposing it to errors generated by the
reciprocal movement or vibration of one pick up with respect to the
other. This
torque meter typology does not allow the measurement of static
moments.
-
-
-
mailto:
info@AdvancedMeasurementSolutions.com
|